12
0
0
Reducing Power Consumption per Unit of Mixture by Optimizing Asphalt Mixing Time
Optimizing mixing time is a crucial strategy for customers seeking to reduce power consumption per unit of mixture in asphalt production. By fine-tuning the duration of the mixing process, operators can achieve significant energy savings while maintaining the quality of the final product. This article explores effective methods for optimizing mixing time, focusing on practical insights from a user perspective.
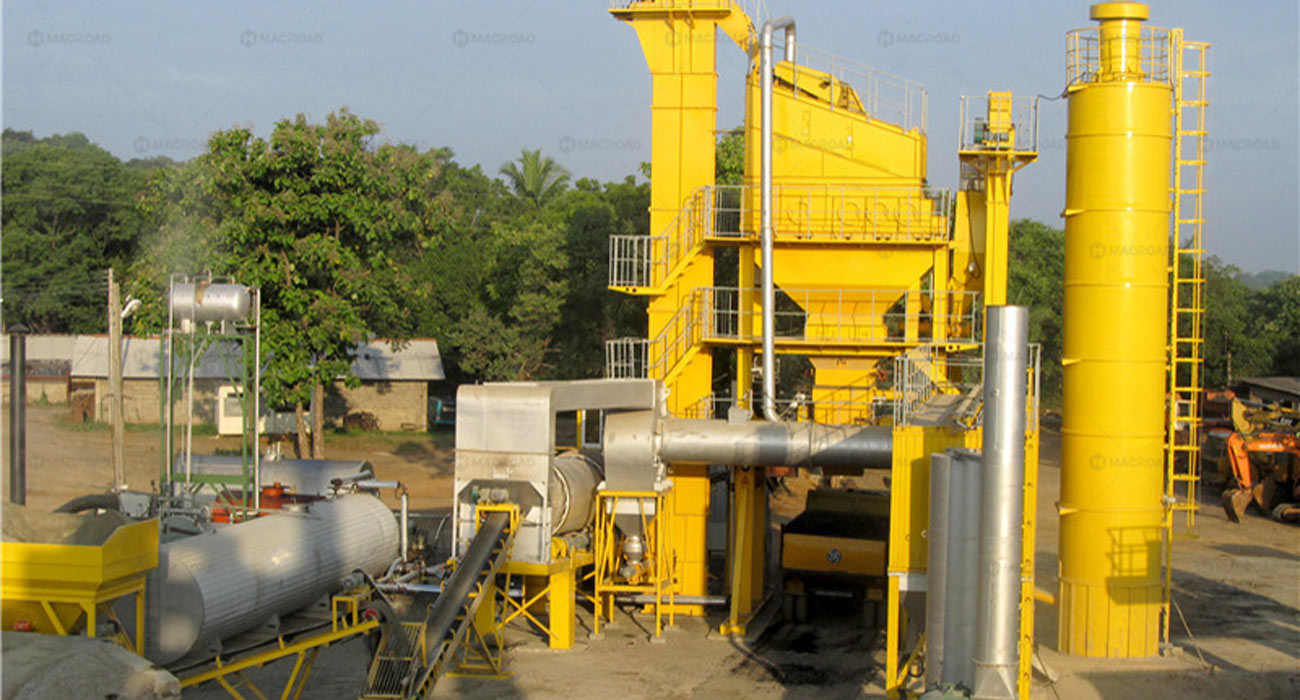
Understanding the Relationship Between Mixing Time and Power Consumption
The relationship between mixing time and power consumption is fundamental in asphalt mixing plants. When the mixing time is too long, not only does it lead to unnecessary energy use, but it can also affect the quality of the mixture. Conversely, insufficient mixing time can result in poorly blended materials, which can compromise the durability of the asphalt.
For example, in fixed asphalt mixing plants, an optimal mixing time ensures that the aggregates, binder, and additives are uniformly distributed. This uniformity is vital for achieving the desired properties of the asphalt, especially in projects such as extremely cold areas road projects, where the material must withstand harsh conditions. By carefully analyzing and adjusting the mixing time, operators can find a balance that minimizes energy consumption while ensuring high-quality output.
Regular monitoring of the mixing process allows operators to identify the optimal mixing duration. Using advanced control systems can help in tracking performance metrics, enabling real-time adjustments based on variables such as material type and environmental conditions.
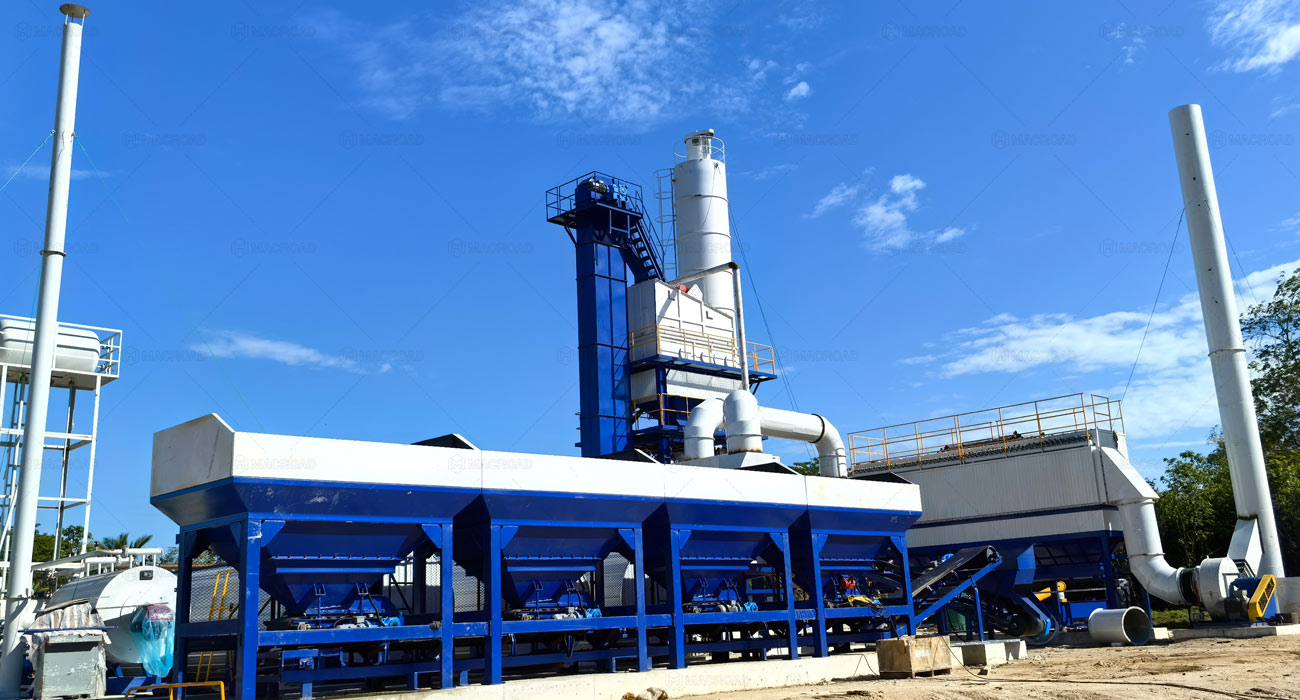
Implementing Advanced Control Systems
To effectively reduce power consumption through optimized mixing time, implementing advanced control systems is essential. These systems can automate the mixing process, allowing for precise control over the duration and intensity of mixing. By using programmable logic controllers (PLCs) and sophisticated software, operators can set specific mixing times based on the materials being used and the desired properties of the final product.
For instance, in a mobile asphalt plant, the flexibility of the control system allows operators to adapt mixing times quickly based on real-time feedback. This adaptability is particularly beneficial in varying conditions, such as when dealing with different aggregate types or during seasonal changes. By utilizing these advanced systems, customers can achieve significant reductions in power consumption without compromising the quality of the asphalt produced.
Moreover, integrating data analytics into the mixing process can help identify patterns and optimize operations further. By analyzing historical data on mixing times and energy consumption, operators can make informed decisions that enhance efficiency.
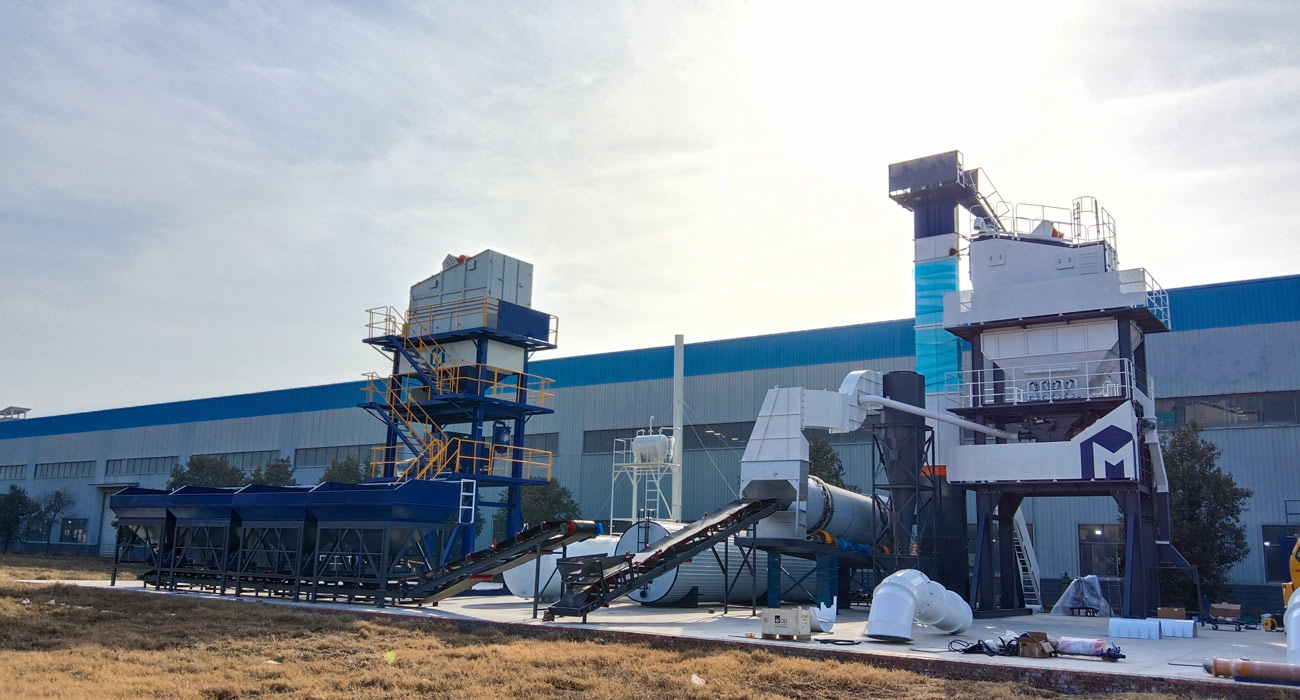
Training and Best Practices for Operators
In addition to technological solutions, training operators on best practices for optimizing mixing time is crucial. Educating staff about the importance of mixing time and its direct impact on energy consumption can foster a culture of efficiency within the plant. Operators should be trained to monitor the mixing process closely and make adjustments as needed based on the type of materials and environmental conditions.
Implementing a feedback system where operators can report their observations and suggestions can also contribute to continuous improvement. For example, if an operator notices that a specific mixture requires less time to achieve the desired quality, this information can be shared with the team to refine the mixing process further.
Additionally, maintaining open communication between operators and plant supervisors ensures that everyone is aligned on the goals of optimizing mixing time. Regular meetings can help address challenges and share successes, creating a collaborative environment that prioritizes energy efficiency.
Conclusion
In conclusion, optimizing mixing time is a key strategy for reducing power consumption per unit of mixture in asphalt production. By understanding the relationship between mixing time and energy use, implementing advanced control systems, and training operators on best practices, customers can achieve significant energy savings while maintaining high-quality asphalt. This proactive approach not only enhances operational efficiency but also supports the sustainability of asphalt production, particularly in challenging projects like extremely cold areas road projects.
Understanding the Relationship Between Mixing Time and Power Consumption
The relationship between mixing time and power consumption is fundamental in asphalt mixing plants. When the mixing time is too long, not only does it lead to unnecessary energy use, but it can also affect the quality of the mixture. Conversely, insufficient mixing time can result in poorly blended materials, which can compromise the durability of the asphalt.
For example, in fixed asphalt mixing plants, an optimal mixing time ensures that the aggregates, binder, and additives are uniformly distributed. This uniformity is vital for achieving the desired properties of the asphalt, especially in projects such as extremely cold areas road projects, where the material must withstand harsh conditions. By carefully analyzing and adjusting the mixing time, operators can find a balance that minimizes energy consumption while ensuring high-quality output.
Regular monitoring of the mixing process allows operators to identify the optimal mixing duration. Using advanced control systems can help in tracking performance metrics, enabling real-time adjustments based on variables such as material type and environmental conditions.
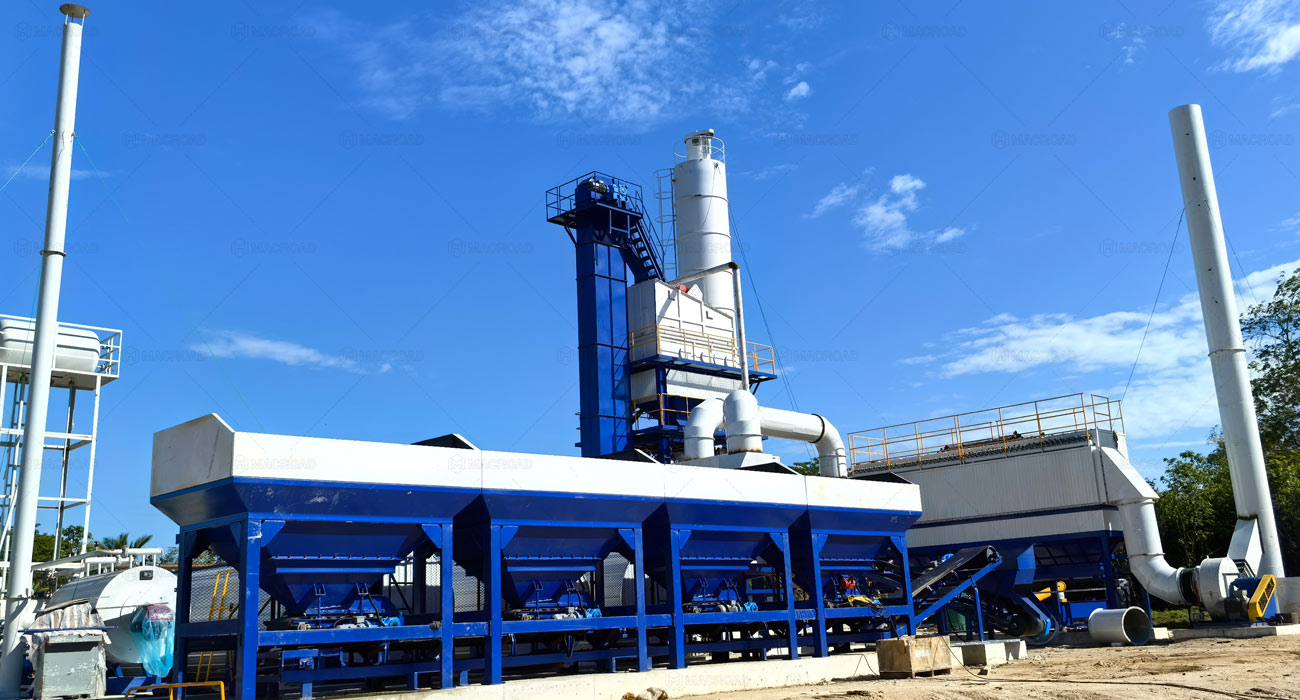
Implementing Advanced Control Systems
To effectively reduce power consumption through optimized mixing time, implementing advanced control systems is essential. These systems can automate the mixing process, allowing for precise control over the duration and intensity of mixing. By using programmable logic controllers (PLCs) and sophisticated software, operators can set specific mixing times based on the materials being used and the desired properties of the final product.
For instance, in a mobile asphalt plant, the flexibility of the control system allows operators to adapt mixing times quickly based on real-time feedback. This adaptability is particularly beneficial in varying conditions, such as when dealing with different aggregate types or during seasonal changes. By utilizing these advanced systems, customers can achieve significant reductions in power consumption without compromising the quality of the asphalt produced.
Moreover, integrating data analytics into the mixing process can help identify patterns and optimize operations further. By analyzing historical data on mixing times and energy consumption, operators can make informed decisions that enhance efficiency.
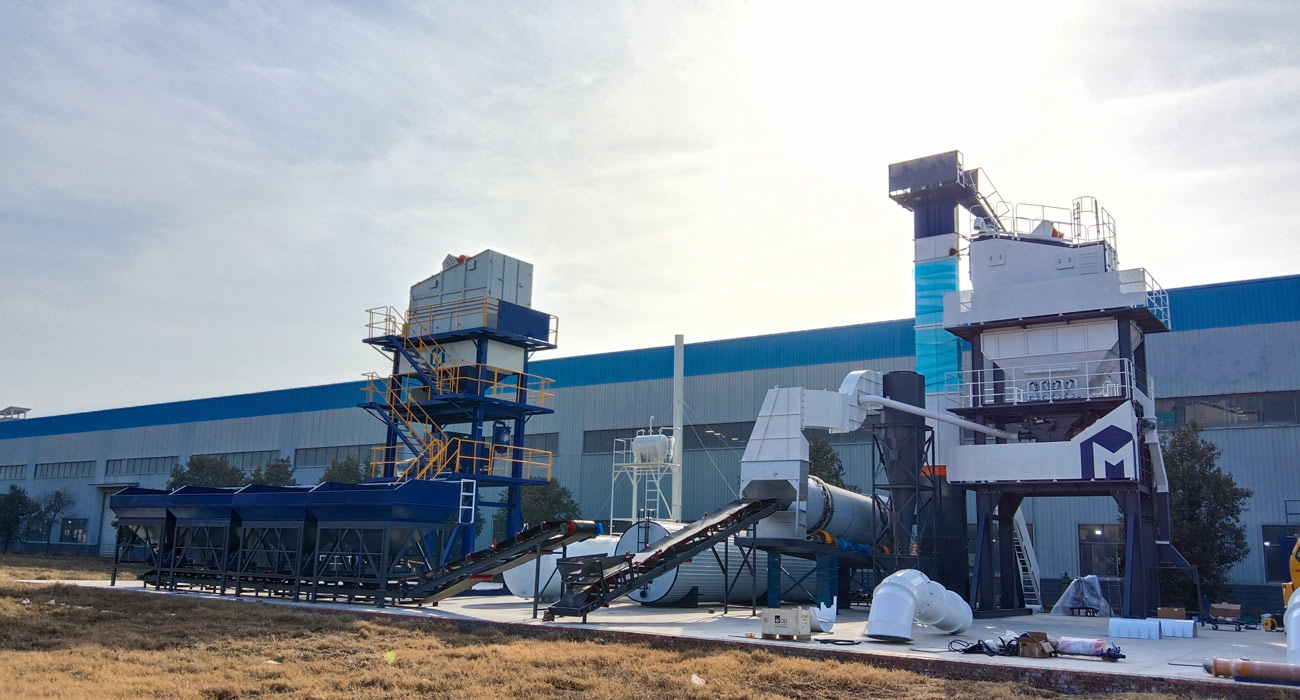
Training and Best Practices for Operators
In addition to technological solutions, training operators on best practices for optimizing mixing time is crucial. Educating staff about the importance of mixing time and its direct impact on energy consumption can foster a culture of efficiency within the plant. Operators should be trained to monitor the mixing process closely and make adjustments as needed based on the type of materials and environmental conditions.
Implementing a feedback system where operators can report their observations and suggestions can also contribute to continuous improvement. For example, if an operator notices that a specific mixture requires less time to achieve the desired quality, this information can be shared with the team to refine the mixing process further.
Additionally, maintaining open communication between operators and plant supervisors ensures that everyone is aligned on the goals of optimizing mixing time. Regular meetings can help address challenges and share successes, creating a collaborative environment that prioritizes energy efficiency.
Conclusion
In conclusion, optimizing mixing time is a key strategy for reducing power consumption per unit of mixture in asphalt production. By understanding the relationship between mixing time and energy use, implementing advanced control systems, and training operators on best practices, customers can achieve significant energy savings while maintaining high-quality asphalt. This proactive approach not only enhances operational efficiency but also supports the sustainability of asphalt production, particularly in challenging projects like extremely cold areas road projects.