10
0
0
Achieving Refined Budget Management in Asphalt Mixing Plants
Effective budget management is crucial for the operational success of asphalt mixing plants. With the growing complexity of projects and fluctuating market conditions, achieving refined control over budgets has become more important than ever. This article explores strategies that asphalt mixing plants can implement to enhance budget management, focusing on precise forecasting, cost tracking, and continuous improvement.
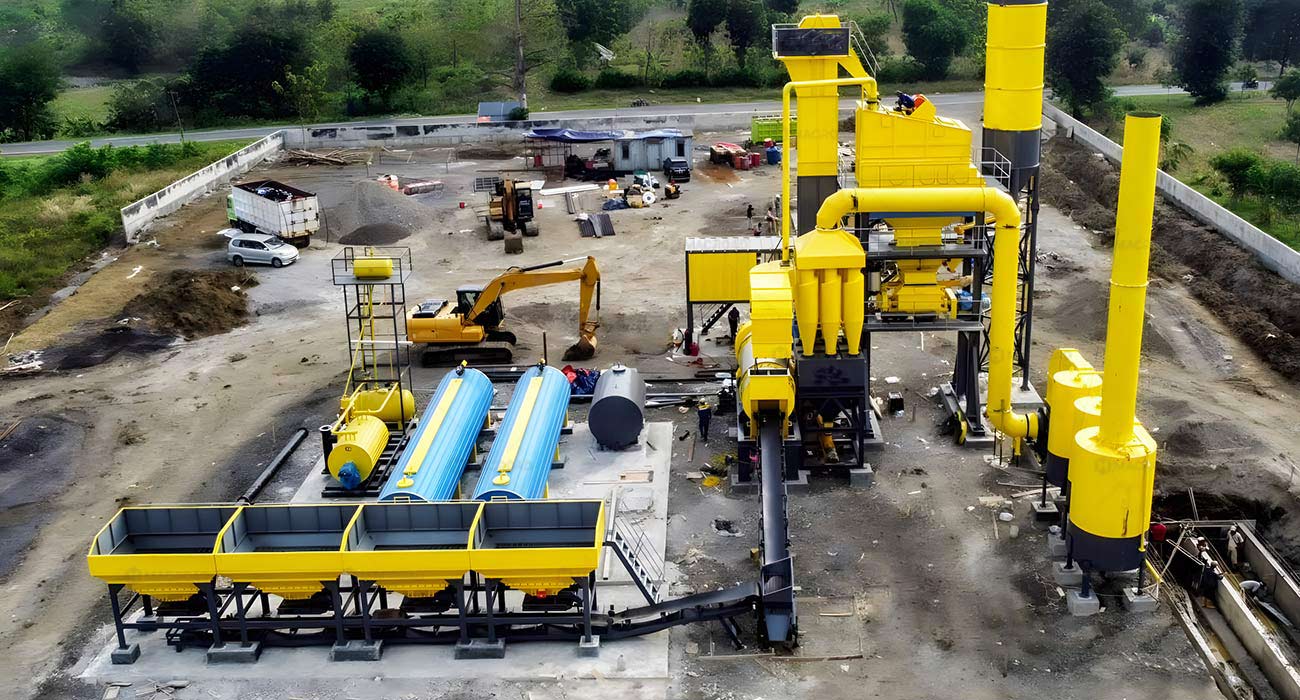
Precise Forecasting for Budget Accuracy
One of the foundational elements of refined budget management is precise forecasting. Asphalt mixing plants need to develop accurate budgets based on historical data, market trends, and project specifications. This involves analyzing past project costs, understanding seasonal fluctuations in demand, and considering potential changes in raw material prices.
For example, if a plant typically uses a mini asphalt plant for smaller projects, it should assess the costs associated with these operations, including labor, materials, and overheads. By creating detailed forecasts, plants can establish realistic budgets that reflect their operational realities. This accuracy allows for better resource allocation and minimizes the risk of overspending.
Moreover, incorporating advanced forecasting tools can enhance this process. Utilizing software that integrates data analytics and machine learning can help predict future expenses more accurately. By leveraging these technologies, asphalt mixing plants can respond proactively to potential budget variances, ensuring that they remain on track financially.
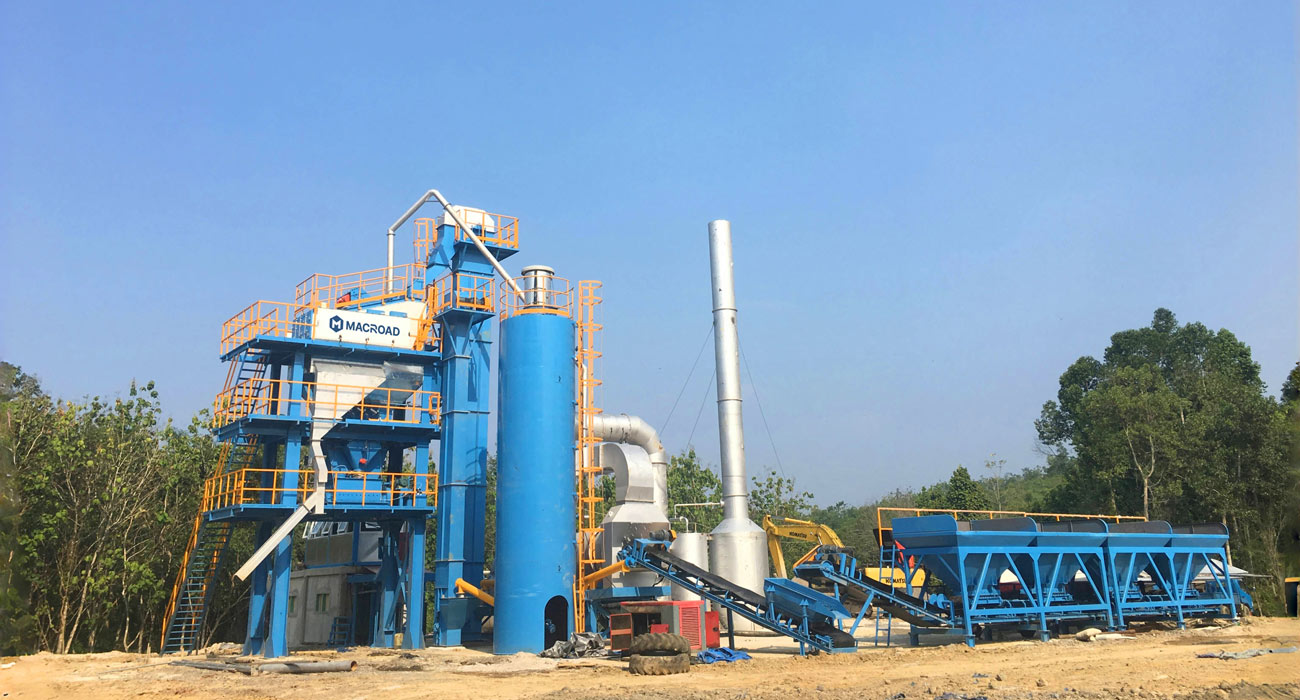
Effective Cost Tracking and Monitoring
Once a budget is established, continuous cost tracking becomes essential for refined management. Regularly monitoring expenses against the budget allows asphalt mixing plants to identify discrepancies early and take corrective actions. This includes tracking costs related to labor, materials, and equipment usage.
Implementing a robust financial management system can facilitate effective cost tracking. For instance, using cloud-based software allows real-time updates on expenditures, enabling teams to access information from any location. This is particularly useful for plants operating multiple sites or those utilizing mobile asphalt mixing plants, as it ensures consistency in financial reporting across different locations.
Additionally, establishing key performance indicators (KPIs) related to budget management can provide valuable insights. Metrics such as cost per ton of produced asphalt or the ratio of actual to planned expenditures offer a clear picture of financial health. Regularly reviewing these KPIs allows management to make informed decisions, adjust budgets as needed, and improve overall financial performance.
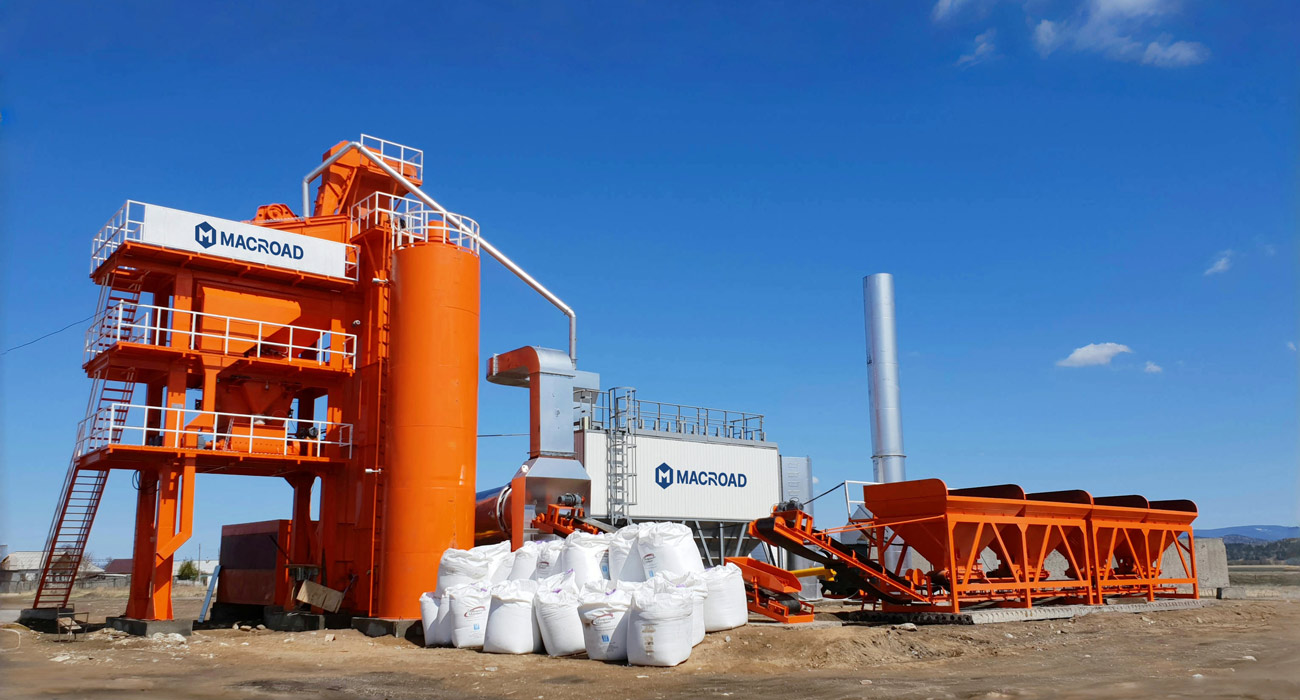
Continuous Improvement and Adjustments
Refined budget management is not a one-time effort but rather an ongoing process of continuous improvement. Asphalt mixing plants should regularly review their budgeting processes and financial performance to identify areas for enhancement. This can involve conducting post-project evaluations to analyze budget adherence and pinpointing factors that led to variances.
Encouraging a culture of feedback and collaboration among teams is vital for this improvement process. By involving employees in budget discussions and seeking their input on cost-saving measures, plants can cultivate innovative solutions tailored to their specific operations. For example, a team might suggest optimizing the use of a fixed asphalt mixing plant for large projects while reserving mini asphalt plants for smaller tasks, ensuring efficient resource utilization.
Furthermore, staying informed about industry trends and economic conditions can help asphalt mixing plants adjust their budgets proactively. By anticipating changes in raw material prices or shifts in demand, plants can better prepare their financial strategies, minimizing the impact of unforeseen circumstances on their budgets.
Conclusion
Achieving refined budget management in asphalt mixing plants is essential for operational efficiency and financial stability. By focusing on precise forecasting, effective cost tracking, and a commitment to continuous improvement, plants can optimize their budgeting processes. As the industry evolves, implementing these strategies will not only enhance financial performance but also position asphalt mixing plants for long-term success in a competitive market. Embracing a proactive approach to budget management will ensure that these plants can navigate challenges and capitalize on opportunities effectively.
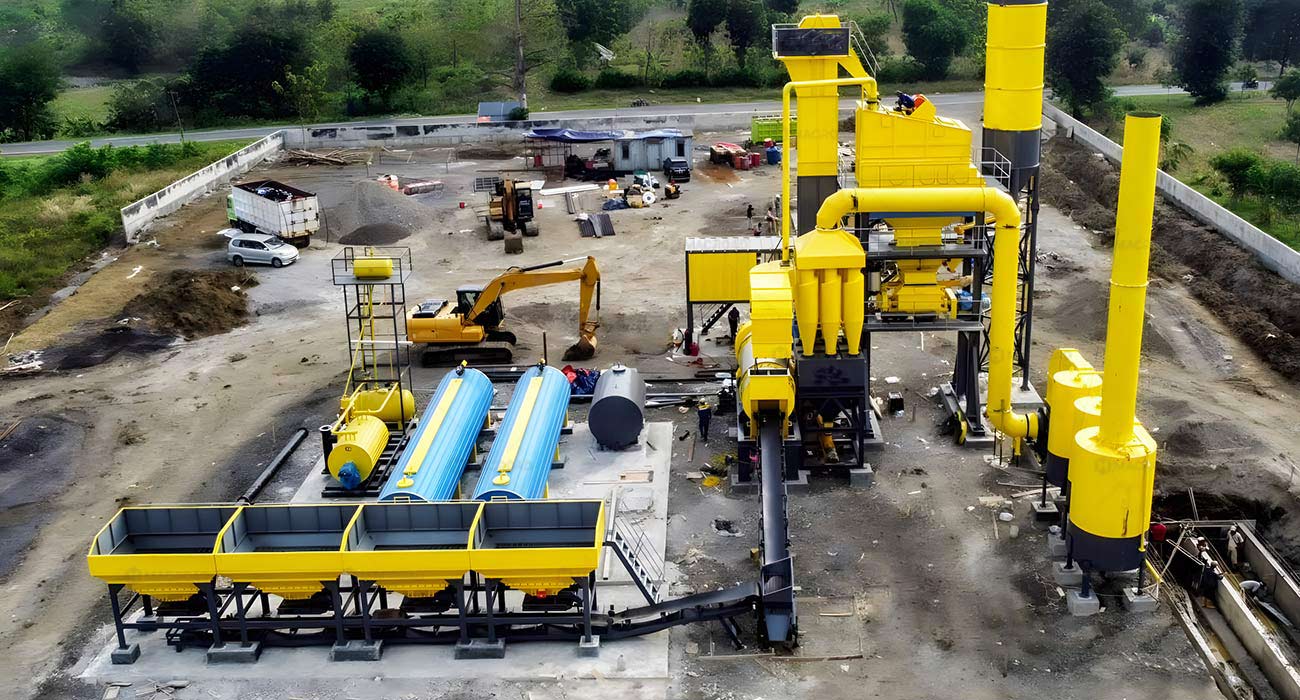
Precise Forecasting for Budget Accuracy
One of the foundational elements of refined budget management is precise forecasting. Asphalt mixing plants need to develop accurate budgets based on historical data, market trends, and project specifications. This involves analyzing past project costs, understanding seasonal fluctuations in demand, and considering potential changes in raw material prices.
For example, if a plant typically uses a mini asphalt plant for smaller projects, it should assess the costs associated with these operations, including labor, materials, and overheads. By creating detailed forecasts, plants can establish realistic budgets that reflect their operational realities. This accuracy allows for better resource allocation and minimizes the risk of overspending.
Moreover, incorporating advanced forecasting tools can enhance this process. Utilizing software that integrates data analytics and machine learning can help predict future expenses more accurately. By leveraging these technologies, asphalt mixing plants can respond proactively to potential budget variances, ensuring that they remain on track financially.
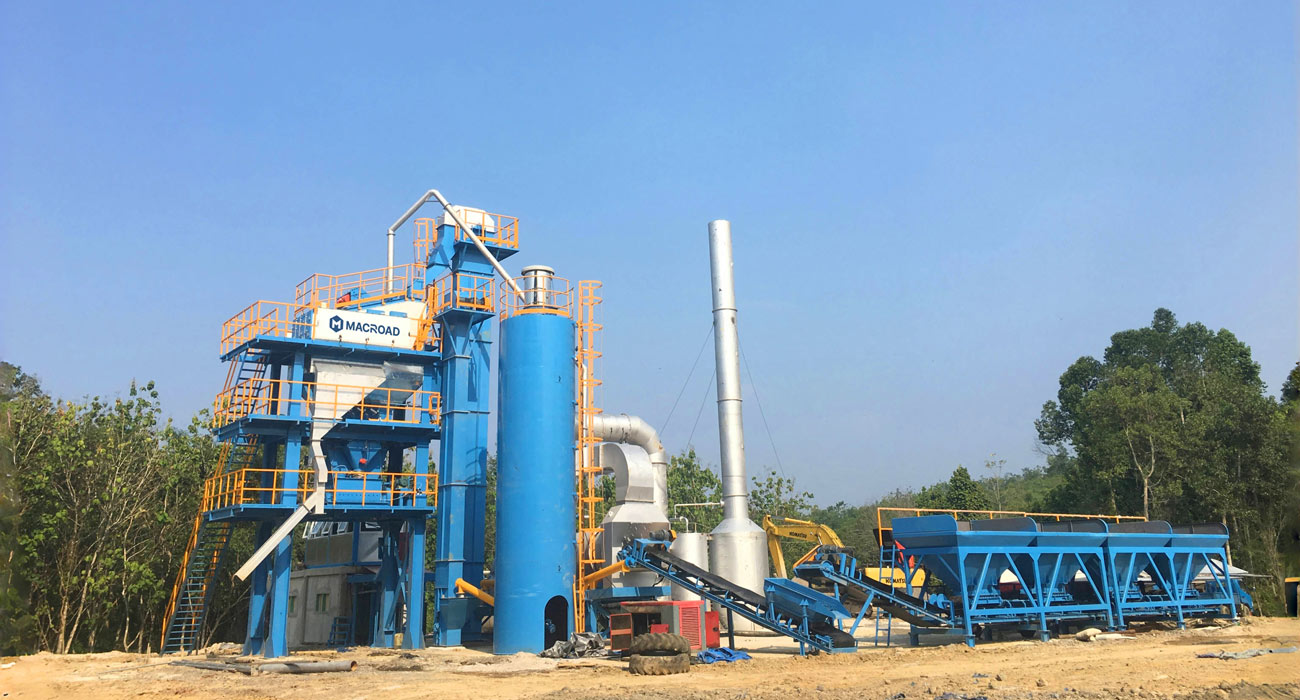
Effective Cost Tracking and Monitoring
Once a budget is established, continuous cost tracking becomes essential for refined management. Regularly monitoring expenses against the budget allows asphalt mixing plants to identify discrepancies early and take corrective actions. This includes tracking costs related to labor, materials, and equipment usage.
Implementing a robust financial management system can facilitate effective cost tracking. For instance, using cloud-based software allows real-time updates on expenditures, enabling teams to access information from any location. This is particularly useful for plants operating multiple sites or those utilizing mobile asphalt mixing plants, as it ensures consistency in financial reporting across different locations.
Additionally, establishing key performance indicators (KPIs) related to budget management can provide valuable insights. Metrics such as cost per ton of produced asphalt or the ratio of actual to planned expenditures offer a clear picture of financial health. Regularly reviewing these KPIs allows management to make informed decisions, adjust budgets as needed, and improve overall financial performance.
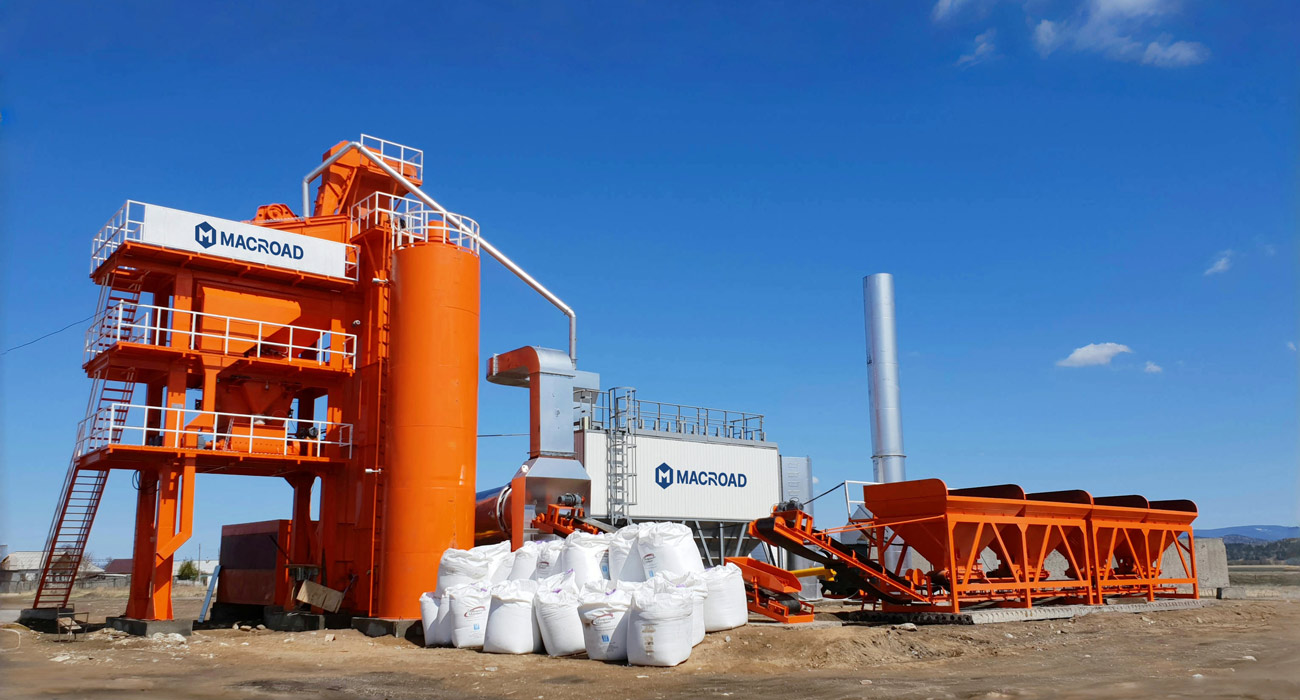
Continuous Improvement and Adjustments
Refined budget management is not a one-time effort but rather an ongoing process of continuous improvement. Asphalt mixing plants should regularly review their budgeting processes and financial performance to identify areas for enhancement. This can involve conducting post-project evaluations to analyze budget adherence and pinpointing factors that led to variances.
Encouraging a culture of feedback and collaboration among teams is vital for this improvement process. By involving employees in budget discussions and seeking their input on cost-saving measures, plants can cultivate innovative solutions tailored to their specific operations. For example, a team might suggest optimizing the use of a fixed asphalt mixing plant for large projects while reserving mini asphalt plants for smaller tasks, ensuring efficient resource utilization.
Furthermore, staying informed about industry trends and economic conditions can help asphalt mixing plants adjust their budgets proactively. By anticipating changes in raw material prices or shifts in demand, plants can better prepare their financial strategies, minimizing the impact of unforeseen circumstances on their budgets.
Conclusion
Achieving refined budget management in asphalt mixing plants is essential for operational efficiency and financial stability. By focusing on precise forecasting, effective cost tracking, and a commitment to continuous improvement, plants can optimize their budgeting processes. As the industry evolves, implementing these strategies will not only enhance financial performance but also position asphalt mixing plants for long-term success in a competitive market. Embracing a proactive approach to budget management will ensure that these plants can navigate challenges and capitalize on opportunities effectively.